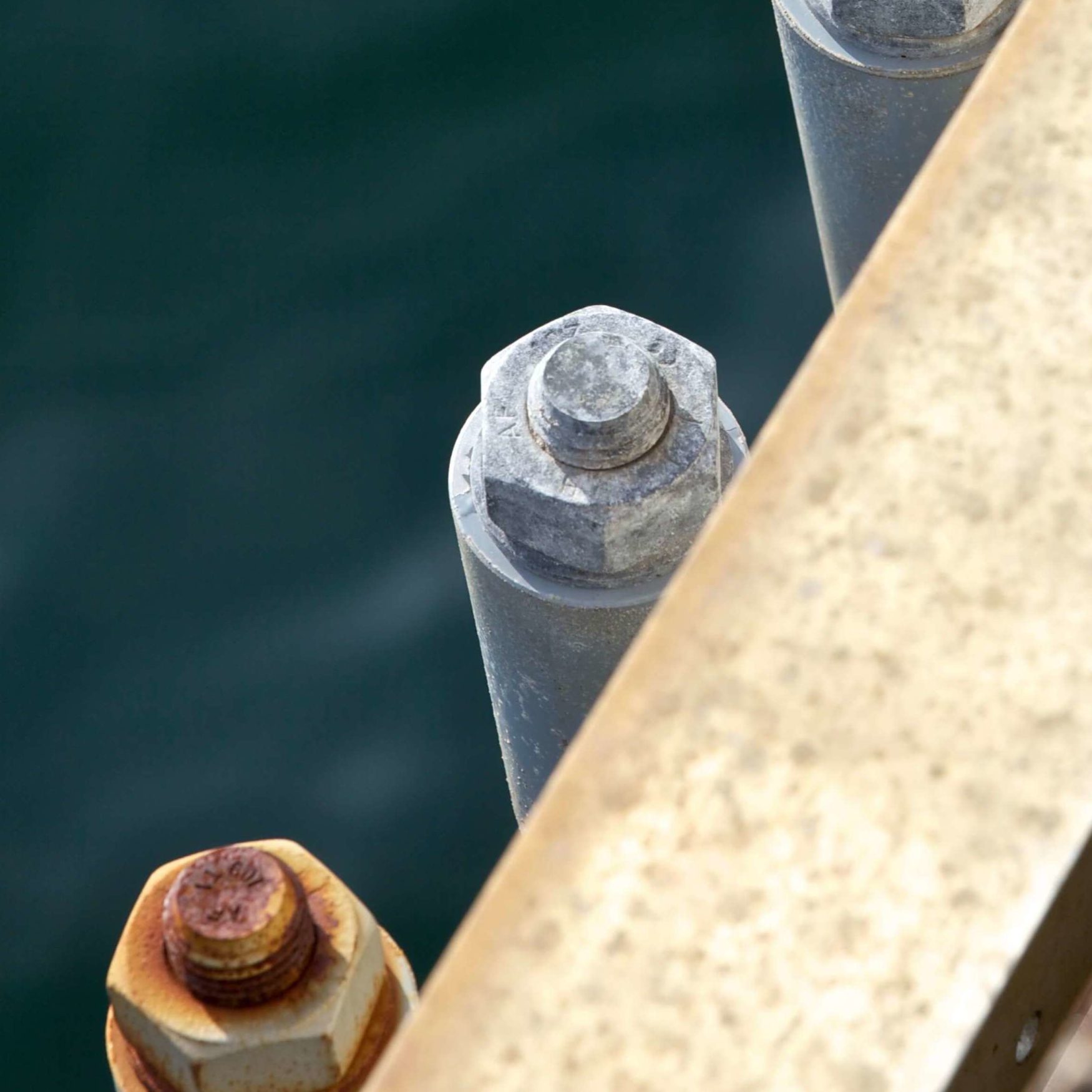
Oxigard is a surface protection for C5-M Offshore use which has been tested and certified under real conditions. The coating process produces highly resistant surfaces for highly corrosive maritime applications. It is significantly more resistant to mechanical stresses than the coatings currently in use. These products are used with particular focus on dimensionally stable materials, such as connectors used in the nacelle area. In addition, coatings of higher strength materials (FK 10 and FK 10.9) are possible, without any subsequent annealing process. This is a functional and economical innovation for the offshore sector.
The development environment of the OXIGARD surface only worked under real conditions
Over two years, WHW Hillebrand and WKLM tested several test specimens with different corrosion protection surfaces in immersion and spray areas on the high seas on Heligoland. There you can find one of the two offshore corrosion test stands in Germany from the Materials Testing Institute (MPA) Stuttgart. Among the surfaces tested was the OXIGARD system developed specifically for this application.
After a storage period of 24 months, the tet specimens were removed under the supervision of Germanischer Lloyd and MPA Stuttgart and the exact corrosion damage and other important physical characteristics, such as the breakaway torques of the individual systems, were determined, documented and evaluated.
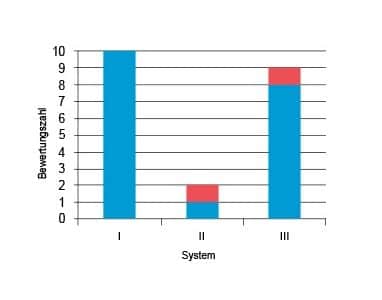
Ergebnisse der zweijährigen Auslagerung unter C5-M-Bedingungen am Teststand Helgoland
„Für maritime Umgebungen sind erfahrungsgemäß Bewertungsgrade größer oder gleich 7 akzeptabel. Das System Oxigard ist aus korrosionstechnischer Sicht für den Einsatz im athmosphärischen Offshore-Bereich einsetzbar. Das System Oxigard zeigt nach der Auslagerung nur vereinzelt einen geringen lokalen Angriff des Grundwerkstoffs. Großflächig liegt die Schichtdicke des Systems auch nach der Auslagerung noch im Bereich der Sollschichtdicke.“ (Quelle: MPA, Stuttgart)
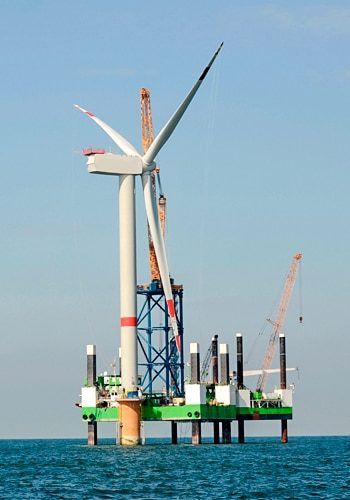
What is so special about the OXIGARD coating process?
Offshore wind turbines are subject to the toughest environmental conditions. This makes both their installation and subsequent maintenance very challenging and expensive. It was therefore necessary to develop a surface which offers impressive corrosion protection while fulfilling numerous advantageous functional properties.
Due to this high demand on the functionality of the surface, any reworking during assembly must be avoided. Such costly work on the high seas includes regrooving the nut thread due to excessive or uneven layer thickness, or the difficult to destructive loosening of connecting elements after the formation of corrosion products. In principle, all processes must be prevented which reduce the corrosion protection and functionality in an uncontrolled way due to damage to the coating system.
The OXIGARD surface has undergone a coating process which has been tested several times and, thanks to the high performance set at delivery, can be directly installed without any reworking necessary at the place the materials are used.
OXIGARD – special functional properties
- OXIGARD offers very high corrosion protection (C5-M certified)
- The layer system has high dimensional stability thanks to the thin and contour-consistent layers
- OXIGARD has negligible setting behaviour thanks to the hard metallic layers (> 400 HV)
- OXIGARD has constant release torques where there is extreme corrosion (see certificate GL-CON 1016HH)
- Defined friction values are set at the factory
- The appearance is silver-coloured, the feel metallic
Certified testing
Testing certified and confirmed according to the corrosivity category C5-M in accordance with EN ISO 12944 Part 2 by Germanischer Lloyd. Confirmation number GL-CON 1015 HH
OXIGARD – technical profile
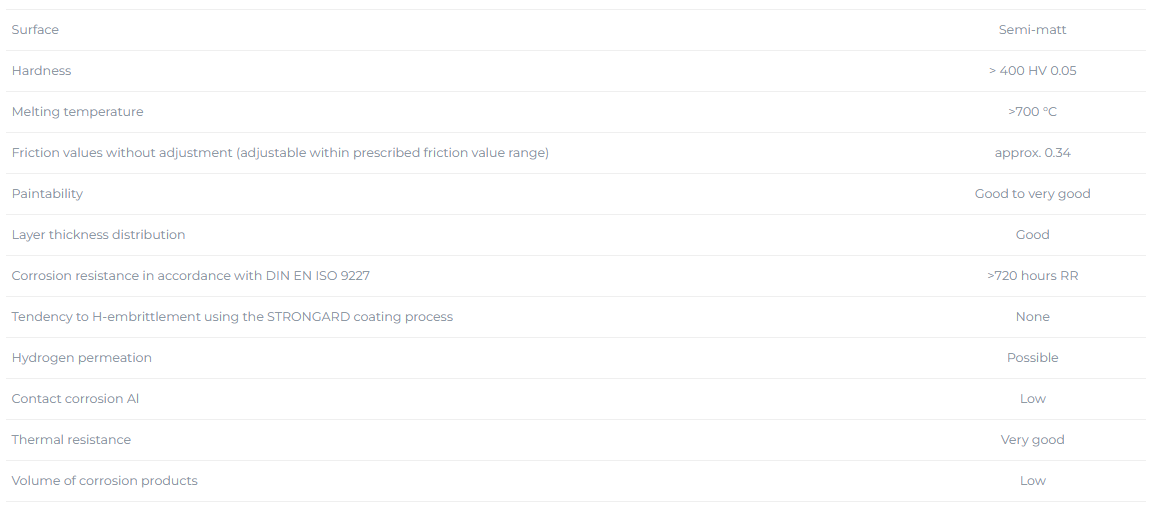